Work Packages
WP1: Traceable accurate techniques for in-situ surface high temperature measurement >1000°C
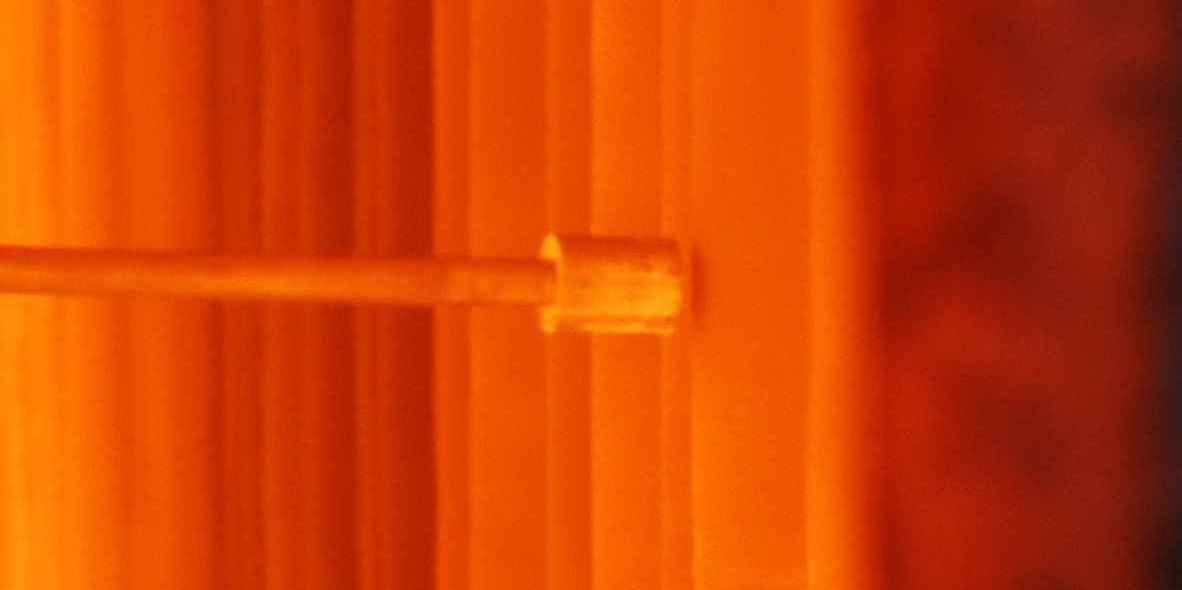
This work specifically addresses long-standing unsolved problems in the application of radiation thermometry in industry, namely solving or mitigating the problems of unknown surface emissivity and varying background reflected radiation. Research is focussed on three very different technical solutions that will give known traceable temperatures at critical points within the process. This would be a leap forward in the application of radiation thermometry in energy intensive industries such as glass, iron and steel and carbon composite manufacture.
WP2: Validated methodology for lifetime and drift tests for contact thermometry sensors >1000 °C
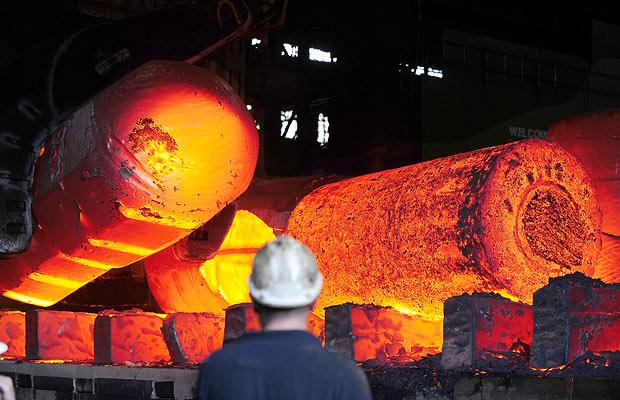
No established capability exists within the NMIs for long-term testing of contact temperature sensors at high temperatures. Some sensor testing has been undertaken by manufacturers but little of that information is in the public domain, and traceability to ITS-90 is often lacking. This WP will establish a capability for standardised drift and lifetime testing of thermocouples (and potentially other temperature sensors) in a manner that is traceable to the established temperature scale, ITS-90. Lifetime and drift assessments are critical so thermocouples are replaced when necessary to ensure continued optimum process control.
WP3: Selfvalidating contact thermometry sensors >2000 °C
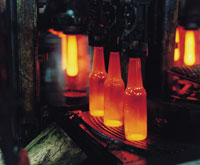
There are currently no high temperature sensors with self-validating capability at these extremes of temperatures. A two-pronged approach is envisaged where the incorporation of known temperature references within special thermocouples and electrical noise thermometry will be developed to probe the stability of conventional temperature sensors. The outcome of this WP is to have qualified methods that will make a step change improvement in high temperature thermometry, for e.g. instead of having to tolerate 20-50 °C uncertainty when using W/Re thermocouples the aim would be at a ten fold improvement to 2-5°C.
WP4: Validated methods for non-contact thermometry >2500 °C with novel correction techniques
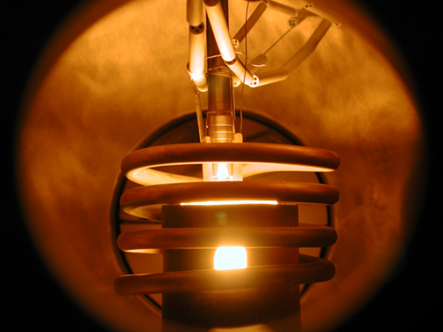
Many industrial processes (e.g. carbon-carbon composite production for train, aircraft and high end car brakes, as well as specialist aerospace and space applications such as thermoprotection and rocket nozzles) are controlled using radiation thermometry. This often necessitates viewing and controlling the process with a radiation thermometer through a window that is progressively getting dirty, diminishing the effectiveness of the process-control. Radiation thermometers can routinely read 50 °C or more too low because of window contamination. This often means that the temperature is increased needlessly "over-cooking" the product (causing potential damage and rejection of the product) and use of excess energy. Moreover, the stability of the radiation thermometer can be affected by the harsh operational conditions and an unquantified drift of the thermometer output can occur. In this workpackage we intend to develop in-situ validation methods based on high-temperature fixed points to address both these problems. These methods will be tested at different levels of temperature (between 1500 °C up to 2800 °C) in industrial, or near-industrial, configurations. By implementing this approach optimal control can be maintained and the stability of the measuring instruments continuously checked; only the energy required for the process will be consumed, leading to consistent quality (and hence zero waste) product.
WP5: Traceable temperature measurements for exotic thermal processing methods
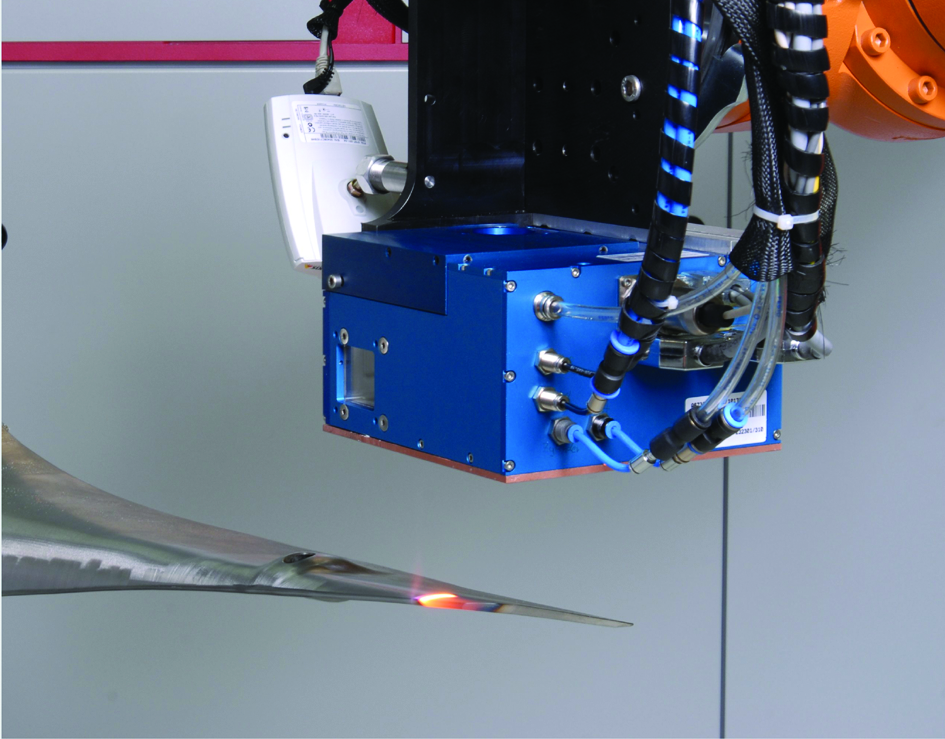
The temperature measurements required for these type of processes are generally solved by bespoke (and hence expensive) methods. On some occasions ad-hoc trial and error methods are used to determine the right process conditions. The scope of this WP is potentially vast so we have decided to focus on a tough industrial challenge of temperature measurement in the field of laser welding/hardening, a materials processing method that is a wide spread in the EU. By establishing, for the first time, reliably traceable high temperature measurements in this field we will be able to use the outcomes of this WP as a case study to demonstrate the improvements that are possible if the new methods developed in this project were adopted by other industrial sectors. New techniques will be used here for the first time used to systematically determine the spectral emissivity for typical metals in industrial conditions for temperatures up to 1500 °C.
WP6: Establishment of reference functions for non-standard thermocouples
No such dedicated capability exists in Europe and as such this WP is a significant step beyond the current state of the art. This WP aims at developing the metrology tools to enable the rapid characterisation of reference functions for non-standard thermocouples to high temperatures - at least to 2000 °C. The lack of reference functions for such sensors has limited their uptake, even though they could be of great use in specialist industries. For the derivation of high temperature reference functions pyrometers, novel high temperature references (eutectic fixed points above 1400 °C) and high temperature furnaces will have to be deployed. Due to the complexity in determining the reference functions it is essential that the high temperature measurement skills of a number of NMIs be brought to bear on this WP. Exotic thermocouples often have poorly determined reference functions with uncertainties of 5-10 °C, the aim of this WP is to radically improve this situation with target uncertainties of order ~1-2°C.
WP7: Knowledge Transfer
Interactive HiTeMS webportal, Articles in trade press, Presentations at trade fairs/industrial conferences, More than 40 technical papers, Annual progress reports to Euramet TC-T, Industrial focussed workshop, Euramet Technical guide on thermocouple lifetime and drift assessment.
For more information: Graham Machin