Case Study:
Dielectric Metrology to Support of Microwave Chemistry - Monitoring of Polymerisation
The Industrial Microwave Group at the University of Nottingham, UK, undertakes research into the application of dielectric measurements to industrial processing. This preliminary study was concerned with their use to monitor chemical polymerisation reactions on-line - in this case the polymerisation of ε-Caprolactone into poly-Caprolactone (PCL).
A common problem with many polymerisation reactions is the current inability to monitor the reaction in real time. Typically, monitoring in industry relies on a combination of off-line testing methods and empirical observations. This leads to inefficient processing in terms of energy and asset use, leading to multi-million Euro wastages across the processing industry. The development of reliable, accurate and traceable on-line monitoring techniques is therefore essential to ensure the best efficiency and quality in the control of the process. Dielectric spectroscopy shows great promise as a potential technique. Previous work carried out at the University of Nottingham1 demonstrated that there is a relationship, at 2.45 GHz, between permittivity (ε') and the PCL molecular weight (Mn) of the ε-Caprolactone polymerisation reaction with time demonstrating it could be employed as an online monitoring technique. This is possible because the ε-Caprolactone monomer has a much higher permittivity and loss than the polymer product, see Figure 1:
![]() |
![]() |
|
Figure 1: Permittivity (ε') at 2.45 GHz and PCL molecular weight (Mn) of the ε-Caprolactone polymerisation reaction versus polymerisation time1. |
Figure 2: Permittivity (ε') of the polymerisation mixture |
The purpose of the Case Study was to investigate the next steps into the practical design of an on-line monitor for this reaction. In particular this work aimed to study what frequencies a monitoring device could work at, to work toward identification an optimum frequency for this monitoring and to adopt a transmission, rather than a reflectometric measurement technique for the monitoring, as described below.
As monitoring techniques will employ low powers they are not limited to ISM bands so the choice of the best monitoring frequency or frequencies can be based on the behaviour of the reaction over a large frequency range. The Industrial Microwave Group at the University of Nottingham measured the permittivity of different proportions of monomer/polymer mixtures from 1 to 20 GHz with a reflectometric coaxial probe technique. From Figure 2 it can be seen that the permittivity increases as the percentage of the monomer ε-Caprolactone in the mix increases. This corresponds to the permittivity decreasing as the reaction proceeds which is in agreement with the data in Figure 1.
Most microwave monitoring processes rely on reflectometric techniques, but these techniques will be inappropriate for the long-term monitoring of this process in reaction vessels. It will be essential to monitor the bulk of liquid across the width of the reaction vessel during polymerisation. Reflectometric probes can only monitor complex permittivities close to their probe tip and in heterogeneous liquid mixtures coatings of chemicals which form on surfaces do not have the same composition as the bulk mixture. Transmission techniques do not suffer from this limitation. To take the first steps towards evaluation of transmission techniques, NPL measured the monomer/polymer mixtures between 8 and 12.4 GHz by transmission in X-band waveguide. The measurements are in agreement with the coaxial reflectometric probe measurements showing that confidence can at least be put in the latter for laboratory tests (as opposed to reaction vessel monitoring) because the NPL measurements are traceable to national UK standards.
Figure 3 shows a comparison of coaxial probe and waveguide measurements:
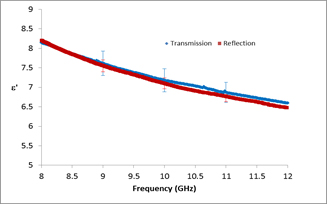
The next steps towards designing an on-line monitor will include a survey of the transmissivity of the reagent mixtures across a wider range of frequencies and temperatures, because the monitoring technique will be required to work at the dimensional scales that the chemical processing demands - too high a loss in the dielectric mixtures will prevent transmission monitoring across a large reaction vessel. Geometries for launching the microwave across the vessel will also be studied. A successful implementation of dielectric monitoring for this system will open the door to its much wider application in the field of microwave chemistry.
References:
- Kamaruddin, M.J., El Harfi, J., Dimitrakis, G., Nguyen, N.T., Kingman, S.W., Lester, E., Robinson, J.P., Irvine, D.J., 2011. Continuous direct on-line reaction monitoring of a controlled polymerisation via dielectric measurement Green Chemistry. 13(5), 1147-1151